A week getting back in the shop
Published 16 Mar 2020
Tags: wenge, workbench, workshop
After what feels like an age (but is in fact less than two months), I have my new workbench installed in my new workshop:
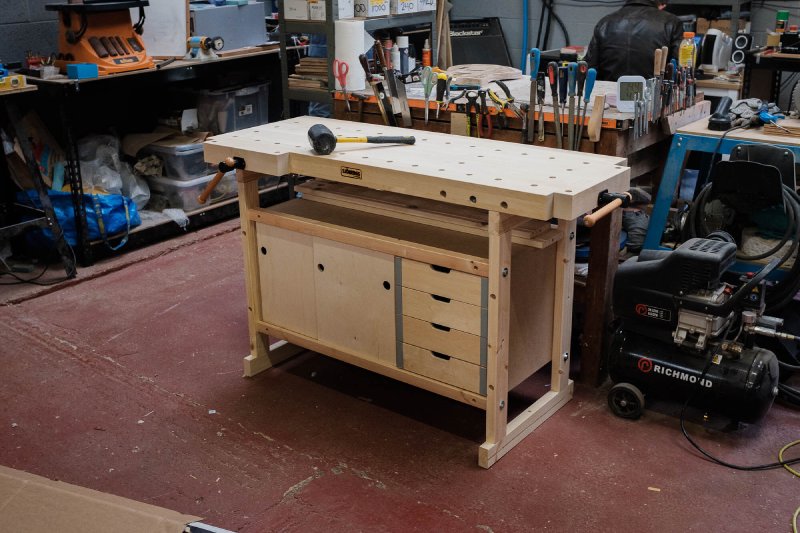
I’m now renting a bit of workshop space from another, more established, local electric-guitar builder, so I’m looking forward to seeing both what I can learn from them and what hopefully I can bring to the workshop having had a different starting point. Due to conflicting schedules I only managed to move in at the end of last week, so I’ve not had time to do much other than assemble the bench itself, but it’s an important step forward, so I’m quite exited.
At the same time I’m aware that I’ve lost momentum this last couple of months since shipping The Green Tiger, and I need to take stock slightly and work out how best to get myself back up to speed in a new environment, where a lot of the assumptions I have about what tools I’ll have to hand etc. will be wrong and I’ll either need to either be borrowing from my workshop buddy, changing my techniques (not again…) or ordering new tools over time to get back to where I want to be as a builder.
I did a start of moving much (but not all) of my bits and pieces out of Makespace at the weekend, so look forward to getting properly installed and productive this week.
The workbench itself, in case anyone is interested, is a Sjoberg’s Nordic Plus 1450. It’s Sjobergs’ upper end hobbyist bench, rather than the low end professional bench which would have been three times the price once you add the similar storage option. Having assembled the bench, I’m happy it’ll be more than sturdy enough for guitar building. I will need to oil it, something I probably should have done before assembly, but I doubt I have space to lay out all the bits to dry, so it’ll have to make do being oiled in place.
Putting the bench together was very easy, so definitely top marks to Sjobergs for that. Whilst putting it together I could overhead some of the non-guitar woodworkers in the same building commenting about it being an Ikea workbench, so I fear I have some reputation building to do in the workshop, but I’m just happy to be up and running and getting on to what I should be doing.
The only thing I had to tweak on the workbench was the handle gaps on the draws were cut a little sharp, so I rounded them off on all the edges with a sanding block just to stop me getting scratches as I open the draws - the work of a few minutes, but makes the draws much nicer to use.
The other thing I want to cover in this week’s notes is a reflection on something I got wrong with one of my earlier builds. It’s always tempting to keep this to myself, as (like most people) I don’t take pleasure in pointing out my failures, but the principle of these notes is to share both the good and the bad, so that others can learn from my experience. Thus I’m going to share with you some feedback I got on one of my earlier builds that’s developed an unfortunate issue, and discuss what we can learn from this.
A week or so ago I sent a message to the people who have an Electric Flapjack guitar to see how they’re getting on. On one hand, I look forward to learning how the guitars get on after they’ve left the shop, as it’s in the hands of customers they really live their lives. At the same time this is always nerve-wracking, as no one wants to be told something isn’t up to the mark; however, you need that feedback if you’re to improve, so it’s important to follow up with clients from time to time.
Overall, the response was positive, but one owner did unfortunately have some some issues to report. He was great in detailing what went wrong, and I’m very grateful to him for how he delivered the news: he made it clear that overall he was very happy, and that he knew he was getting a prototype build that I made early on to try new techniques (and indeed the price reflected this), but wanted to make sure I was aware of the issues he’d hit with this early build so as to help me avoid them in future. If you’re going to have customers tell you bad news, this was the kind of customer you want to do so.
The issue he reported was that a few of the frets have started to work their way loose, and will need replacing, which is clearly not good. The owner is planning to get those frets re-done locally to fix this: the guitar is quite a long way from me, so I think the best cause of action is to get the re-fret done locally if possible (to both save the guitar being put through the post twice, and to support a local guitar tech who will then be there in future if needed), but I have sent as many details on what I did to help that person, and if the client can’t get a local person that I’ve obviously offered to do the job myself to make good what I didn’t get right the first time. Hopefully we can get this guitar back to full health quickly.
But for the purposes of this blog lets take a look at what has most likely caused this issue. Here is a picture of the fretboard in question, taken as I was putting the frets in back in 2018:
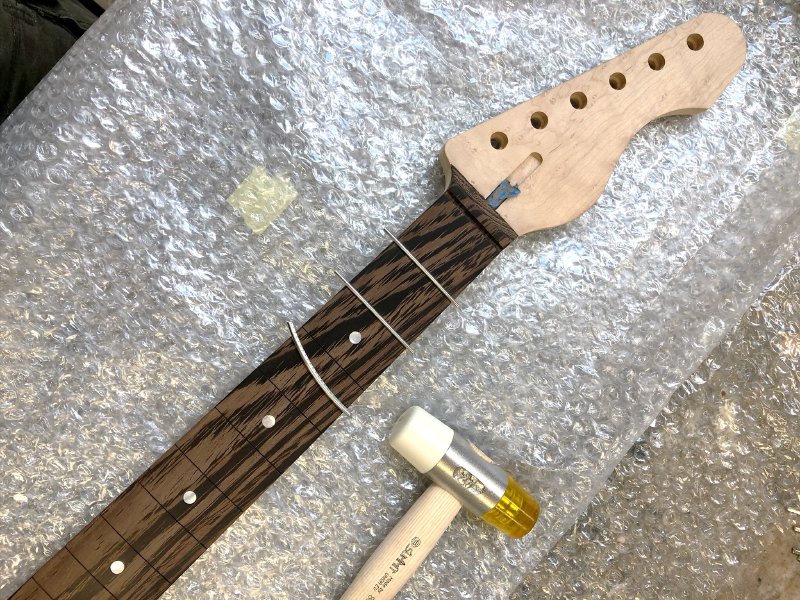
The fretboard here is made from wenge, which is very attractive, but a bit of a particularly troublesome wood to work with. The two different colours you can see in the wood have very different characteristics: the dark wood is very hard, and the light wood is quite soft. This makes it hard to work with generally, but normally the grain is packed quite tightly so you have lots of thin lines of each type, making it overall have a uniform density, as it was on this recent build:
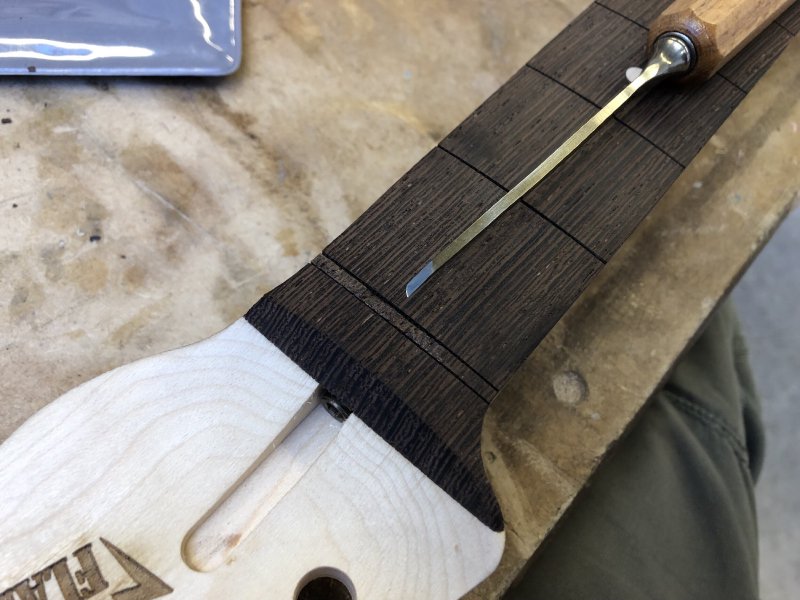
But, as you can see in the original picture, the light/dark patches on the problematic neck are quite large, and there’s a particularly large patch of softer wood on the left hand edge around the middle of the neck (the bottom left in the photo), and I think this is the reason this neck is having issues. That said, it’s not the wood that is the issue here, but how I failed to account for this particular piece due to lack of experience.
When I shipped the guitar, the frets were homed properly, but I do remember getting them there was quite challenging and caused me a good amount of stress. As you can see from the picture, I was using a hammer to get the frets in, and that’s all I was using - not an unusual technique, but perhaps on reflection not necessarily the right one for this bit of wood. The issue with the softer wood is that as you hit it down at one side it’ll tend to lift on the opposite side if the wood hasn’t gripped the fret well enough. With this neck I had to be very careful with the bend I put on the fret-wire (you can see the unseated fret above has a curve on it) before hammering it home to stop it bouncing out the softer parts when I hit particularly hard. At the time I just put it all down to my technique (or lack thereof), not having enough experience to know that this bit of wenge was unusual in its make up.
Even though I got all the frets home in the end, this experience was enough to convince me there had to be a less stressful way to put the frets in, and why I subsequently changed my technique to use an arbour press to push the frets in, which provides an even high pressure over the entire fret, rather than using the hammer. So I’d already learned something from this neck, just not in time for this client unfortunately.
The second thing that didn’t help was I didn’t use glue, which given the issues I was having, in hindsight was a a mistake. Whilst using glue on frets isn’t uncommon, in general (and somewhat ironically) I try to avoid using glue as it makes re-fretting the instrument in later life easier. Frets do have a finite like (usually though we’re talking ten or more years even on a well played instrument), so will need to come out eventually, and I was trying to make that task easier. As it was, I think the soft wood here definitely needed glue to help hold the frets steady, and my lofty principles about some mythical future compromised the instrument’s play-ability in the present.
So there’s two concrete lessons you can take from this unfortunate fret job - but I’ll offer you a third learning, and one that I only got through learning that reviewing this incident has made me realise: I should have rejected this piece of wood. Unfortunately I didn’t understand what issues were in the future for this instrument, but if I got a bit of wenge like this now, I’d pass it over for another piece that has a much more tight and uniform distribution soft and hard grains. Not that there’s anything wrong with the wood in this example, but why make life harder for yourself when fretwork is difficult enough as it is?
So, there you have it - I made a mistake, and I hope sharing this will save you from similar mistakes if you’re a builder too.
Mostly though, I share this just to try and normalise the fact things do occasionally go wrong no matter how much you try to protect against it, and that you shouldn’t let that put you off - you just need to try do right by your mistake if it’s with someone else, and learn as much from it as you can.
And finally, I’d like to say thanks once more to the client for taking the time to give me the feedback to help me grow - I really do appreciate it, you’re a star for doing so.