A week in the shop
Published 11 Mar 2018
Tags: amp, blues deluxe, fusion 360, makespace, red rocker
Thanks to the snow thawing out, bits for guitars #5 and #6 started arriving: the wood and the basic hardware that will attach to it (the bridges, tuners, etc.). So this week has been mostly about getting those guitar builds moving.
First up, the selection of wood arrived from Exotic Hardwoods UK Ltd. With guitars #3 and #4 I went to a local lumber yard for the body and neck woods, and got the fingerboards from random other places on the Internet to suit the build. This time I went to Exotic instead for everything, and someone was asking why not continue to use the local lumberyard as that must be cheaper.
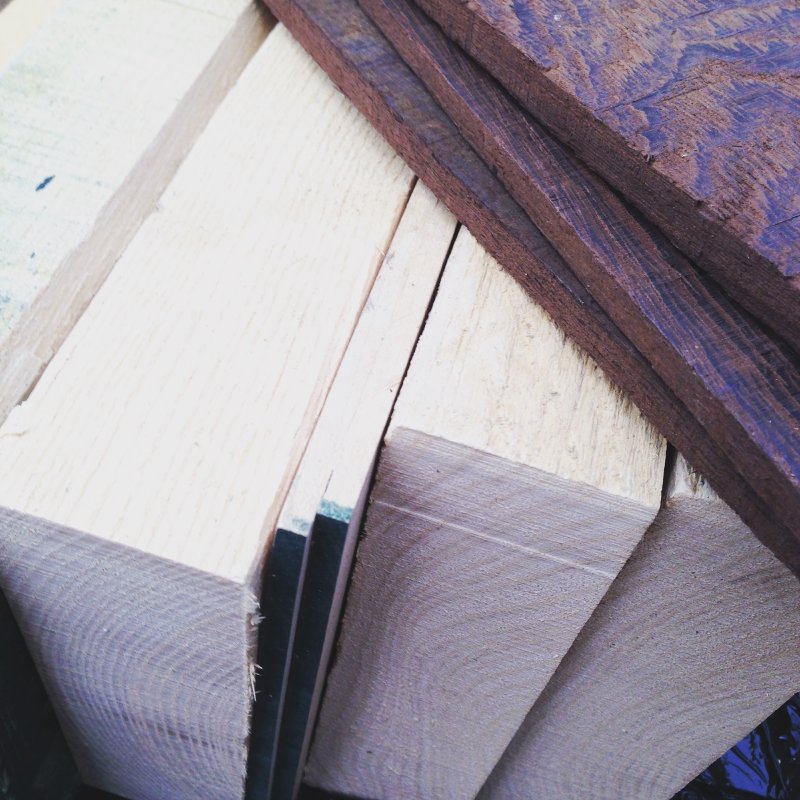
Firstly, whilst the local lumberyard has some nice basic ash and maple, but it’s actually a pain to get to the workshop. The lumber yard is about 20 miles away from Makespace, and they don’t have the facilities to cut it for me into rough bits that will fit in my car, so I’m in the lap of the gods a little when I go in terms of can I get bits I can transport: we only have a small car, so I can’t fit a plank longer than 2.3m in the car, and most their lumber is longer. Indeed, the last time I went I came home empty handed as the shortest plank they had was 2.5m. So whilst buying pre-cut sections of ash is more expensive, it’s way more practical even if it does close to double the price.
Another reason is the selection of woods: the kind of Ash I can buy at the local lumber yard is standard American Ash and this can be quite weighty. Whilst some people like that, indeed that was part of the specification for guitar #5, some people don’t, and for guitar #6 the customer wanted a lighter guitar. For this I’ve gone for the more expensive Swamp Ash, which is notably lighter than American Ash, but also not the kind of thing that you get in the run of the mill lumber yard in the UK that’s supplying mostly builders. Thus going to somewhere like Exotic made sense, and a fellow luthier I know has been very happy with the Swamp Ash they get from Exotic.
Similarly for the necks, although the maple I got from the local lumberyard was perfectly fine for regular necks and quite cheap (a fiver a neck for the raw material!), it’s the same problem transport wise, and for both guitars #5 and #6 both customers wanted something premium maple wise, so we’ve gone with some birds eye maple which has lovely figuring in it, and really for that you do need to go to a specialist wood supplier.
With the wood acquired, it’s time to start making parts for the guitar. Guitars #5 and #6 represent an important step for me as a luthier: for the first time I’m using my own drawings rather than using existing templates. So although the guitars are based on an existing guitar design (the Fender Mustang), I measured and drew the designs myself in Fusion 360.
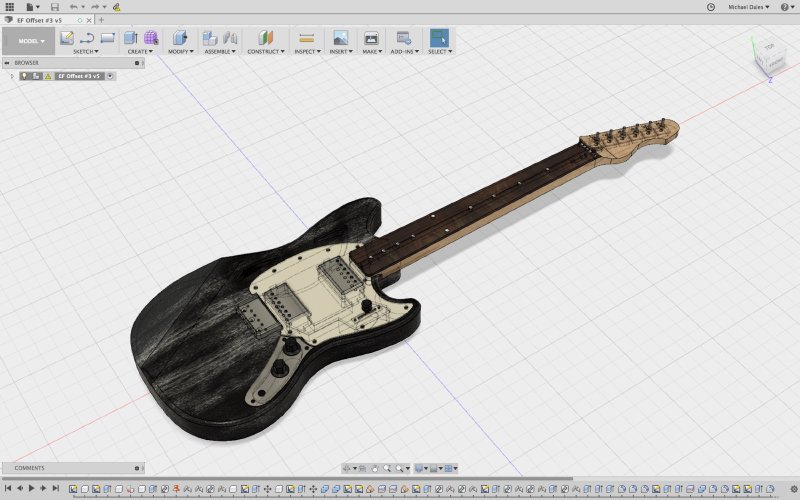
Moving to Fusion 360 is quite a change workflow wise. Until now I was feeding 2D drawings into the CNC router software we have at Makespace which supported just basic 2D operations such as outline, pocket, and drill. Fusion 360 gives you much more flexibility, but requires a different way of thinking about things. So, before I let loose on the lovely birds eye maple, I took an existing maple neck blank I had and set out to carve a neck from my new designs. The more astute regular readers may note that I’m now making prototypes for the prototype guitars :)
The neck design I’ve gone with here is different from what I’ve done in the past for my teles. Partly, this is due to practical reasons: Mustang’s have a shorter 24" scale length compared to the 25.5" scale length on a tele or strat, which means a shorter neck, which means a standard truss rod won’t fit in in exactly the same manner. At the same time, I was never happy with the truss rod access on the tele’s I’ve made (or indeed owned), both in terms of it being fiddly to get right in construction, and it’s fiddly to use. I much prefer the access offered on some other guitar makers I’ve seen, such as those of Fidelity Guitars and Titan Guitars. So using those designs as inspiration, these necks will have the truss rod end exposed for easy access and adjustment, so it’s more functional, and it simplifies the construction a little to let me build the necks more accurately.
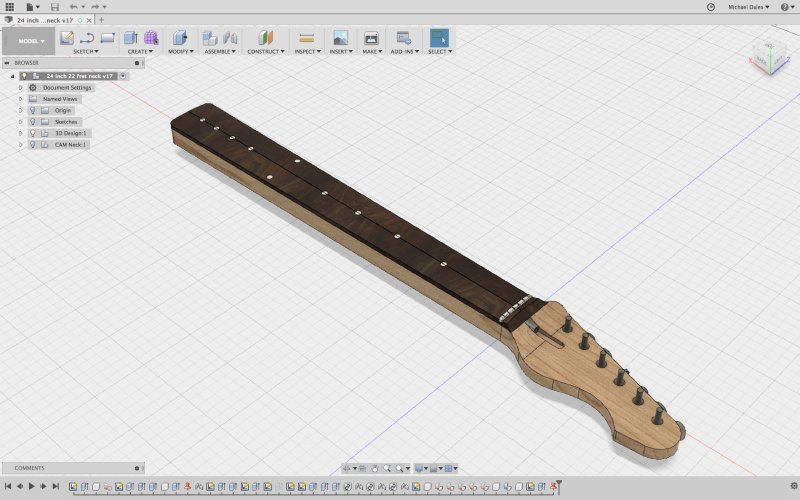
One of the other things I wasn’t happy about with the previous necks was how I made the curved transition between the headstock and the fretboard. Ideally you’d use a drum sander to get the radius there, with a jig to limit how you can move the neck ensure you don’t take too much away. Makespace doesn’t have a drum sander unfortunately, so I’d been using a drum sanding drill bit fitted to the pillar drill as a work around. This got the job done, but was hard to use with a jig due to the plate on a pillar drill not being as big as on a drum sander, and I ended up having to spend a bunch of time trying to correct the end result until I was happy with it. This time around (as I previewed the other week) my plan has been to carve the transition on the CNC router. Because Fusion 360 is a 3D CAD and CAM tool, I can actually get Fusion to generate 3D tool paths for the CNC router, and so this seemed like a sensible place to take advantage of that.
You obviously get into the is it hand made if you CNC route it debate here, but ultimately whilst I’d love to do this by hand, I just don’t have the right tools right now, and it’s way more important to me that customers get a guitar they’re happy with than did I hand shape every single last bit of it. One day I’ll have a drum sander, but for now, this is the best way to make something I’m happy shipping to someone.
Thus this week I sat down for a good few hours to nurse the CNC router as I made my first neck from my new design:

With any new CNC router plan, you really do need to sit and watch it do every cut, as you don’t know what the software will make of your design. Indeed, during this cut I had to stop it several times and go back and tweak my approach to the routing as I learned more about how Fusion likes to do things. But in the end, we got there.
I’m really pleased how it came out. The headstock design is my own that I’ll use for all Electric Flapjack guitars that have tuners on one side, and I think that’s come out good: it’s not too flashy, but also different from what a traditional guitar of this type would have so you know it’s a custom guitar rather than an original. The headstock transition has come out great; after the experiment the other week I got a ball end mill to do just this bit rather than using the same end mill I use for the rest of the carve, and that curve is wonderfully smooth as a result. I can definitely recommend investing in a ball end mill if you need to do curved surfaces when routing.
Next week I’ll make a fretboard for this, and if that goes well I can make the actual necks for guitars #5 and #6 after that.
I also spent some time jointing the guitar body blank for #5. Whilst you do get guitar bodies made from a single piece of wood, it’s more common that they’ll be made of multiple pieces just due to the practicalities of getting a reliable source of wood big enough and at a reasonable price. So as with guitars #3 and #4, guitars #5 and #6 will have two piece bodies. To ensure the parts glue together well, you need to make the edges as level as you can, and for that I break out my #7 jointing plane (#7 refers to the size). It’s a labour intensive few hours, and boy did I feel it the next day, but the parts had a lovely close finish and is ready for getting to the right thickness and routing.
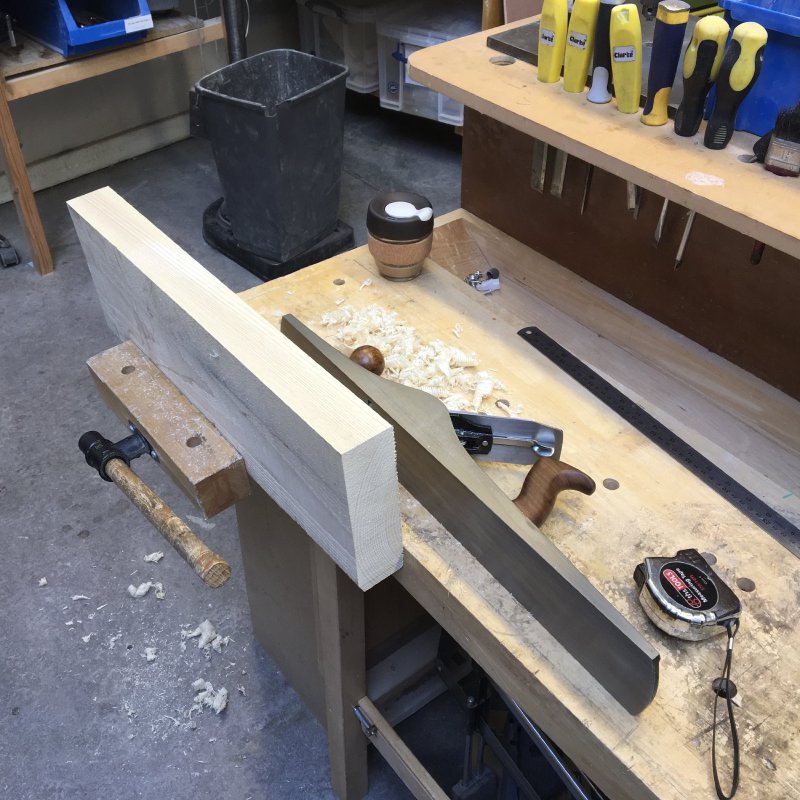
Closure on the amp construction: it is now fully finished! Last week I’d got it all working except the neon power indicator still wasn’t working, even though I’d bought a replacement bulb. During the week a third bulb turned up from a different supplier, and that worked!
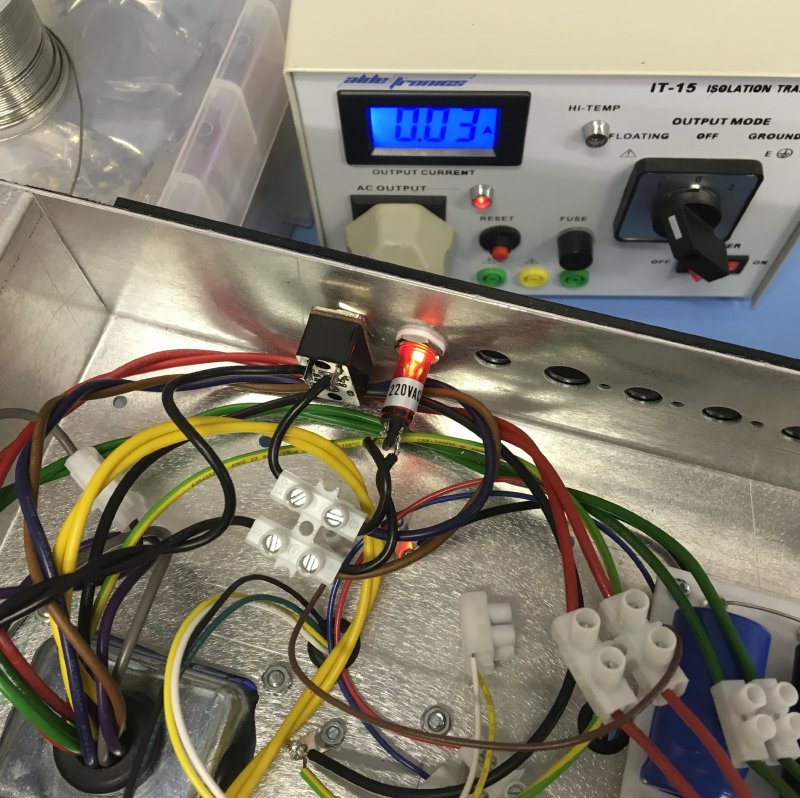
My assumption now is that the original supplier unfortunately had a duff batch. I’ve let them know; less that I’m worried about a refund for a component that costs less than a pound, but more so that they can check the rest of their supplies before shipping them to others. It could still be me of course, perhaps I accidentally overheated the old bulbs whilst soldering them, but for now all I really care about is the amp is finished and I can shortly take it home and make it my daily amp.
The reason I’m not taking it immediately home is because I’d have to bring it straight back to Makespace in a couple of days for the show and tell events, where I’ll be exhibiting a couple of my guitars and the amp, and explaining how I used the various bits of kit at Makespace to build them. One of the days is a Makespace members only party to celebrate Makespace’s 5th birthday, but on Thursday 15th there’s a public open night at Makespace as part of the Cambridge Science Festival, so if you want to see me in my workshop environment, do come along to that.
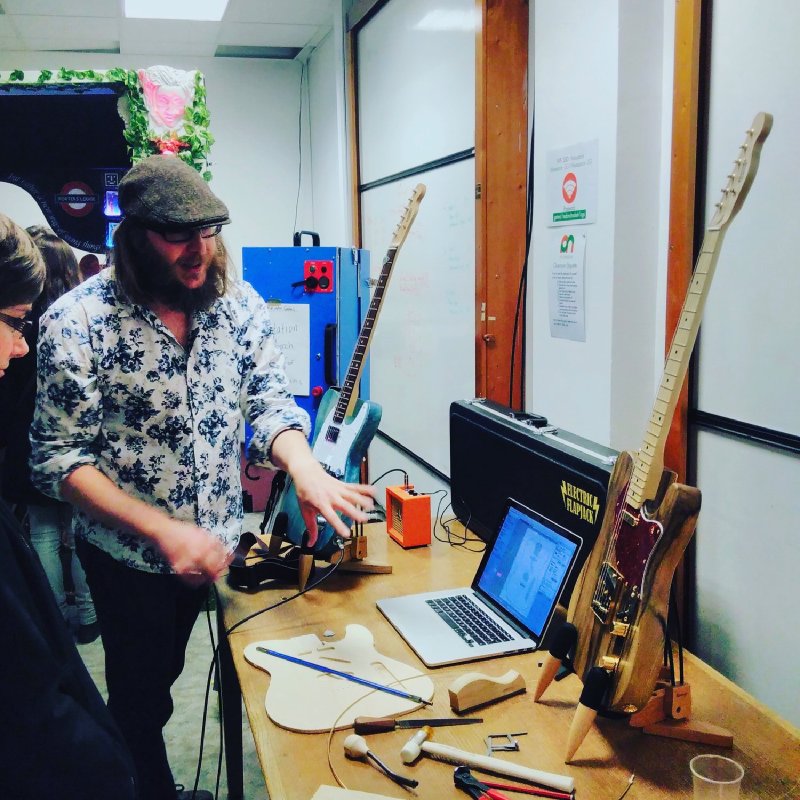
But that’s not all!
On March 21st I’ll be giving a talk at the CamCreatives meet up about how I got started in making guitars from having no experience, a bit about what’s involved, and generally trying to encourage people that stepping into a totally new field is very doable if you just approach it right. The meetup invite for that should be up shortly, and I’ll post here when it does.
I’m also very excited to announce I’ll be part of Liverpool MakeFest again this year, which will be on June 30th at Liverpool Central Library. I’ll have a stand showing off some guitars and bits of in-progress guitar and trying to explain to people how they too can make things. I did this last year, and it was a wonderful day talking to people about building things, and trying to encourage people that whilst making things may seem daunting, but again really isn’t if you just start small and work your way up.
I still find it amazing that two years ago I’d never made a guitar, and I hand’t done woodwork in over 25 years since high school. I get a kick out of trying to show people who see my guitars and think “I could never do something like that” (be it guitars or whatever their passion is) that it’s just taking the right approach to starting something new that they too can do this sort of thing. So if you have a meetup for such you’d like me to do such a talk, do let me know!