Mapping out a new path to getting back into the workshop
3 Jun 2021
Tags: 3D-printing, concepts, design
It’s been a while hasn’t it? I hope you are keeping safe and well and as sane as can be in these awkward times.
Once again I was forced into hiatus thanks to lockdown and other things, but it seems things are starting to happen again on the guitar building front so I wanted to get back to documenting things again. Whilst I’d like to return to week notes, although I don’t feel like I’ve been doing much this last half year of interest, when I went to write up what I had been doing it turned out I had a lot I wanted to get down, so rather than jumping straight back into weeknotes, the next few posts will be more of a small series of catch-up posts about different topics I’ve been working on, that will hopefully then settle down into a more traditional workshop diary again.
Today’s post is mostly about the broader plans about how I approach guitar building and my planned change in direction, but we’ll dive into more technical specific details on things in future catch-up notes, fear not.
When I started to thinking about returning to the workshop in April, I decided I wanted a new plan rather than just doing more of the same. Whilst I’m pleased with the guitars I’ve made to date, as I mentioned during the brief stint last year when it looked like things were starting up again before the winter hiatus, I know there are specific areas where I need to improve, and I want to figure out a way to let me concentrate of those things. Put another way, how do I spend in my limited workshop time working on the areas I need to improve, and not spend it going back over old ground where I’m already comfortable?
For the answer to his I took inspiration from this small display I set up in my home office to remind me of what life was like before lockdown (and to remind me there is a life beyond perpetual zoom calls):
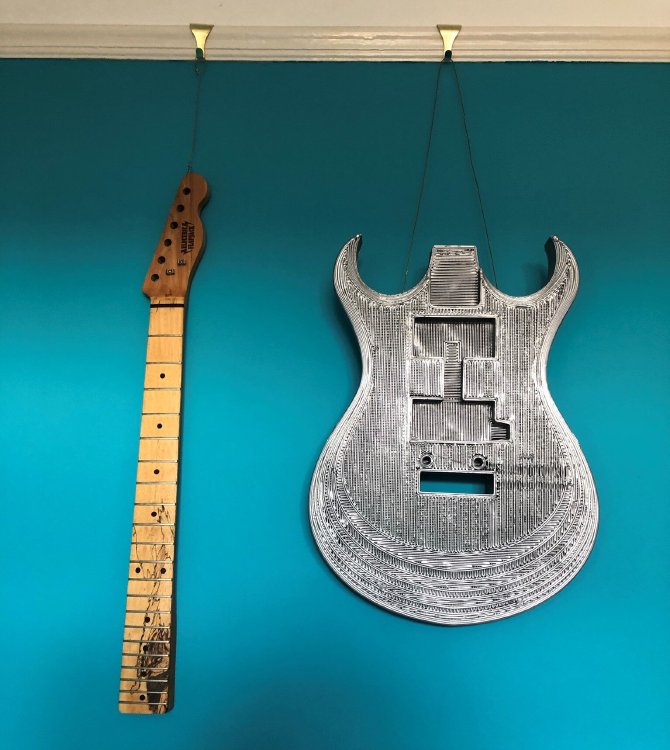
As I alluded to in last fall’s posts, the main area where I want to up my game is in building necks. The neck hung here on my wall is the first neck I made, and it’s hung on the wall because after using it for a couple of years I eventually replaced it with a better one: this one had a slight bow to it that made it awkward to play as I got to be a better guitarist, and as I got to be a better guitar builder I knew I could replace it with something better. It’s a shame not to play it as I really love the patterned wood on the fretboard, but ultimately an instrument is made to be played not admired.
The new neck I built to replace it is a notable improvement, as one would hope, but I still don’t feel I’ve got to the stage where I’ve either got the details down to where I want them or I’ve made enough that I’m confident that it’s readily repeatable. This aligns with the feedback I got from earlier guitars too: any niggles are around the neck. The neck is the root of all the sounds your guitar makes, and the main part where you interact with it when playing, so improvements here really do pay dividends for the entire instrument.
In contrast, the guitar bodies I feel I have down relatively well. There’s always room for improvement of course, or to expand into new areas of woodwork (my long term goal is really to build arch top jazz style guitars one day), but for now I feel of the two halves to a guitar, I can do a better job at this end than the other. So the question is then how can I spend less time making the guitar bodies, as whilst they’re mechanically much simpler, doing them well is still a significant investment in time (if you’re making them by hand as I am). I don’t want to buy in existing bodies, which would be one option, as that doesn’t feel then like I’ve made the guitar. I could try going back to using more CNC machining, but the display on my wall led me to a different conclusion: 3D printed bodies.
Back in 2019 I had the good fortune to have this guitar body I’d designed 3D printed by Liz Bishop at an event I attended at the University of Warwick. Whilst this particular body was only intended as a size and ergonomics guide, rather than something I could use in a real guitar, it’s not that far from being playable with a few tweaks, and that got me thinking about a few direction to take: to let me spend more time on the necks, can make some guitars where I 3D print the bodies?
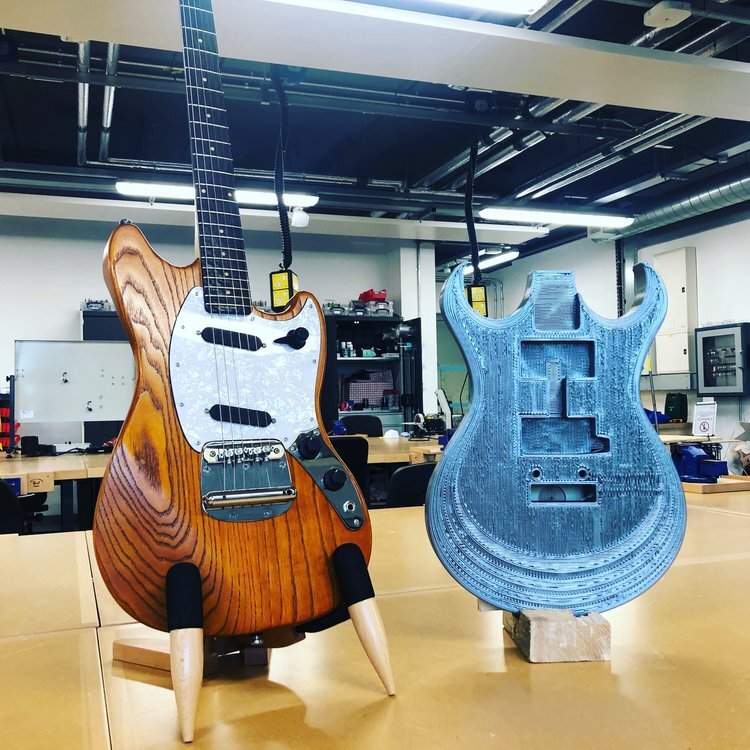
This thought also resonated with another series of musings I’d been having during this hiatus as to why should I go back to building guitars? What is it, as Jimmy Page put it in It Might Get Loud, that I’m bringing to the table? It’s been a fun path to follow the few years before the pandemic, but having effectively had a year away from it, I wasn’t sure why I’d get back to it given the stress and heartache involved in each build when out there are already lots of people doing the same thing better.
Whilst I’m immensely proud of the guitars I’ve built to date, I feel need to find a way to build something that reflects my interests, as conflicting as they may be: I love the raw analog nature of a classically designed electric guitar plugged into an amp just on the edge of breakup - it’s so basic in principle yet so tactile and makes playing all about how the player interacts with the instrument; yet at the same time I am technologist by nature, and I am fascinated by the way high-end production techniques like additive manufacturing, generative design, and so forth have become accessible to people like us rather than just people like Ford or Boeing.
With the guitar builds to date I’ve deliberately tried to keep the instruments themselves very traditional, as I’m aware that’s an easier sell to most guitarists (just look at the fun Gibson had with robotuners) and at the same time I wanted to prove (at least to myself) that I can make a traditional instrument by hand, I’m not just hiding behind the computer to control CNC machines.
But I don’t feel I have that to prove as much now, and so I’d like to explore some alternative approaches to guitar design that I find interesting, rather than just stick with tradition. And whilst the general guitar buying public may then be less interested in what I build, they we’re not really going to notice me anyway as yet another small builder in a sea of small builders, so for that I take inspiration from this coffee mug I picked up in San Francisco to help me cope with stressful work situations:
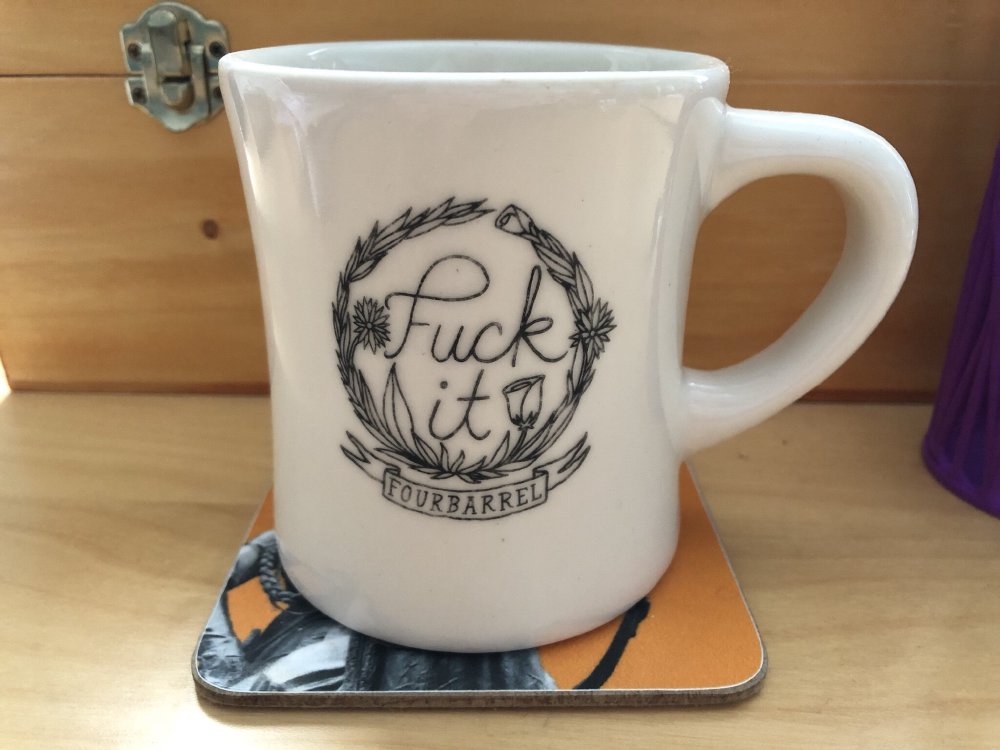
So it’s time to try something new, but what does that look like?
With all this floating around in my head, I set out to do a bunch of simple concept sketches. It’s rare I allow myself time to do things like this (I encourage everyone to do more of this), but I had some downtime where I stepped way from the computer for a week or so and just used my iPad and Pencil, and I just drew guitar ideas - some whole guitars, some just little elements of guitars. At first they all seemed silly and I’m terrible at drawing, but over time a consistent thread of ideas started to emerge. I guess what I’m trying to say is that if you ever think this sort of design process isn’t for you, just work at it and don’t be put off by your feelings about the quality of your sketches - it’s about letting ideas evolve rather than making something beautiful.
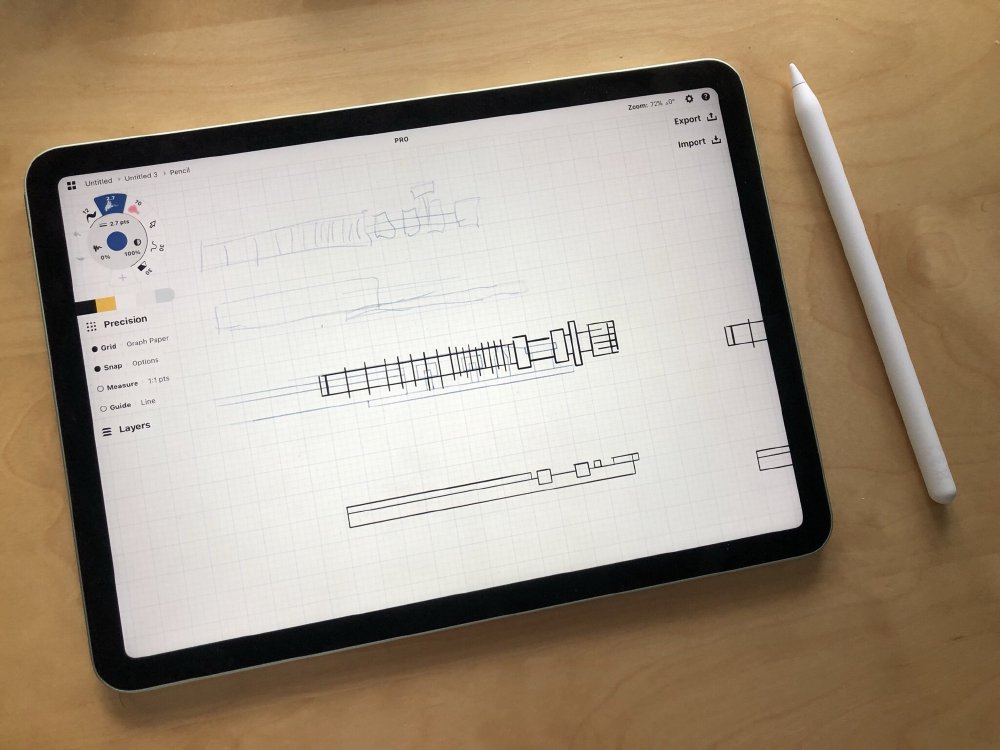
The app I used for the most part was Concepts App, which I remember picking up a few years ago and not getting on with it that well. But the current incarnation has a really nice blend of free hand sketching and guided drawing. It took me a little while to find the best way to mix the two for how I wanted to work, but by the end of it I’d made some nice sketches (some of which I hope to share in time). I think like any tool like this you want to fire it up and be immediately producing works of art, but they all require some level of initial investment. Thankfully they have some really good tutorial videos which helped me get started quickly.
Once I had gone through a bunch of iterations, I turned to Fusion 360 to make a quick 3D model sketch of the first guitar design that incorporates all the ideas I’ve been having, and where hopefully a new guitar building journey beings:

What do you think? Yay or ney? I suspect this will be a bit marmite :)
The idea of this design is to have a central wooden core that runs all the way through the instrument, and then have 3D printed wings that provide the body. This structure of a central core and attached body style isn’t new, it’s actually a reasonably common way you see a lot of custom guitar builds go, only they use wood for the wings rather than 3D printing them, and is usually referred to as a neck-through guitar. It’s particularly effective visually when people use a neck made of laminated contrasting coloured woods and you get to see that run from the headstock to the tail of the body. For me, this approach means that I have a strong central core to which the strings attach at both ends, which avoids the need to worry about how strong my 3D prints are given guitar strings are held to a tension of around 10 to 20 kgs each. Whilst the 3D printed body I have above is quite sturdy, it’s effectively a hollow shell so I doubt it would stand being strung up.
In terms of structure of the 3D printed part, I wanted it to both be a mix of the familiar and show off the nature of the medium: I want it to still be recognisable as a guitar (for now), but I also want to do something different with the material rather than pretend it is a wood substitute. I have some other ideas on how to shape the body, but to let me get up and running quickly as I try to work out how feasible this is, I’ve actually reused the same design that we 3D printed before at Warwick, as I know that design works ergonomically thanks to that initial print. I’ve always had a soft spot for low poly vector art, and for the weird organic like nature of generative designs, so this seemed like an opportunity to try mix those two techniques and make a design that looks somewhat striking.
Because the 3D printed body will be significantly lighter than an wooden one, I was concerned with how this would impact the centre of gravity for the guitar. A guitar typically has a reasonable amount of weight in the headstock thanks to the tuning pegs and you need a slab of wood to support them; indeed even on traditional wooden bodied guitars there’s some designs out there where they end up being headstock heavy, making them unbalanced when you’re trying to play them on a strap (e.g., the Gibson SG). So I’ve decided to, at least for now, make this design headless - the neck will stop at the end of the fretboard and the tuners will be down on the bridge. In general this is seen as a very “metal” thing to do, but I think it’s time we claim this as just another way to design a guitar and manage its weight. I think the traditional guitar headstock has many advantages as a user interface in terms of how easy it is to understand and use, but it’s also not the only option out there, and I’d like to explore the others.
At this stage it’s important to understand that the above is just a sketch: just because I’ve made a crude CAD model doesn’t mean I can build it. The model I have is missing lots of important details, so the next stage is the traditional engineering one of de-risking it, and to keep refining it to the point where I know either I can build it or I need to go back to the drawing board. I’ve started this already, and that’ll be the next catch-up note where we have a look at the work I’ve been doing on the 3D printed body design.
I could also totally fail heading down this route, and spend a lot of effort trying to design something that turns out to be no good as a playable instrument. But that’s okay, for the first time in a year I’ve been eager to make progress again, I’m building something that I feel is more me, and I can feel I’m bringing something to the table now (even if that just is a coffee mug with a crude slogan on it :).